Main Characteristics and Applications
High wear resistance hot-working steel, also be used for wear resistance and polished plastic moulds.
Steel is easy to machine in the annealed condition and needs a hardening process before final machining.
This steel also shows excellent toughness and high level insensitivity to thermal shock and thermal fatigue. A nitriding surface treatment
can be carried out to increase the life of the tooling.
Main applications:
• dies for the pressure casting of light alloys.
• wear resistance plastic moulds.
• tooling for the extrusion of light alloys and steels.
• hot work shear blades.
• rolls for profiling tools (welding area).
• Forging dies.
Hot working tools should be preheated to temperatures in the range 250 – 300°C before use.
Comparable standards
DIN | W.Nr | AISI/ASIM | JIS |
---|---|---|---|
X40CrMov5-1 | 1.2344 | H-13 | SKD61 |
Chemical composition (typical; in weight %)
C | Si | Mn | P (max) | S (max) | Cr | Mo | V |
---|---|---|---|---|---|---|---|
0.35-0.42 | 0.80-1.20 | 0.25-0.50 | 0.03 | 0.03 | 4.80-5.50 | 1.20-1.50 | 0.80-1.15 |
Critical points
Ac1 860 °C
Ac3 940 °C
Ms 340 °C
Production technology
EAF – LF – VD - Forging – Heat treatment +EFS
US specification
In according to standard EN10228-3 Class 4 and standard SEP 1921 Class E/e
Delivery condition
WW.NR. 1.2344 is delivered in annealed condition (EFS), with hardness max 230 HB (21 HRC)
Physical properties (reference values)
20°C | 100°C | 250°C | 500°C | |
---|---|---|---|---|
Thermal expansion coefficient (10-6/K) | 11.3 | 11.6 | 12 | 13 |
Thermal conductivity (W/mk) | 18.8 | 19 | 22.9 | 25.1 |
Young modulus (Kn/mm2) | 212 | 209 | 197 | 175 |
Heat treatment
TREATMENT | TEMPERATURE | HOLDING TIME (HT) | COOLING | COMMENTS | |
---|---|---|---|---|---|
Annealing | Heat to 850 °C | Min. H.T. for 2 minute /mm | Furnace up to 550°C than in air | - | |
Stress relieving | Heat to 650-700°C | Min. H.T. for 2 minute /mm | furnace up to 300-350°C | To be carried out after machining, is recommended to eliminate the residual stresses induced by mechanical working | |
Hardening | Preheating to 350-400°C Second preheating to 750-850°C Heat to hardening temperature to 1000-1020°C | Min. H.T. for 1 minute /mm | Air or pressure gas by vacuum | Quenched hardness 52-56HRC | Tempering | In the range 550 – 600°C for at least 3 h according to hardness requirements and conditions of use. Tempering must be repeated a second time at a temperature equal to or 20°C lower than the previous. Before tempering, the parts must be preheated to 200 – 300°C | Air | Usual service hardness: 44-52 HRC |
C.C.T. Curve
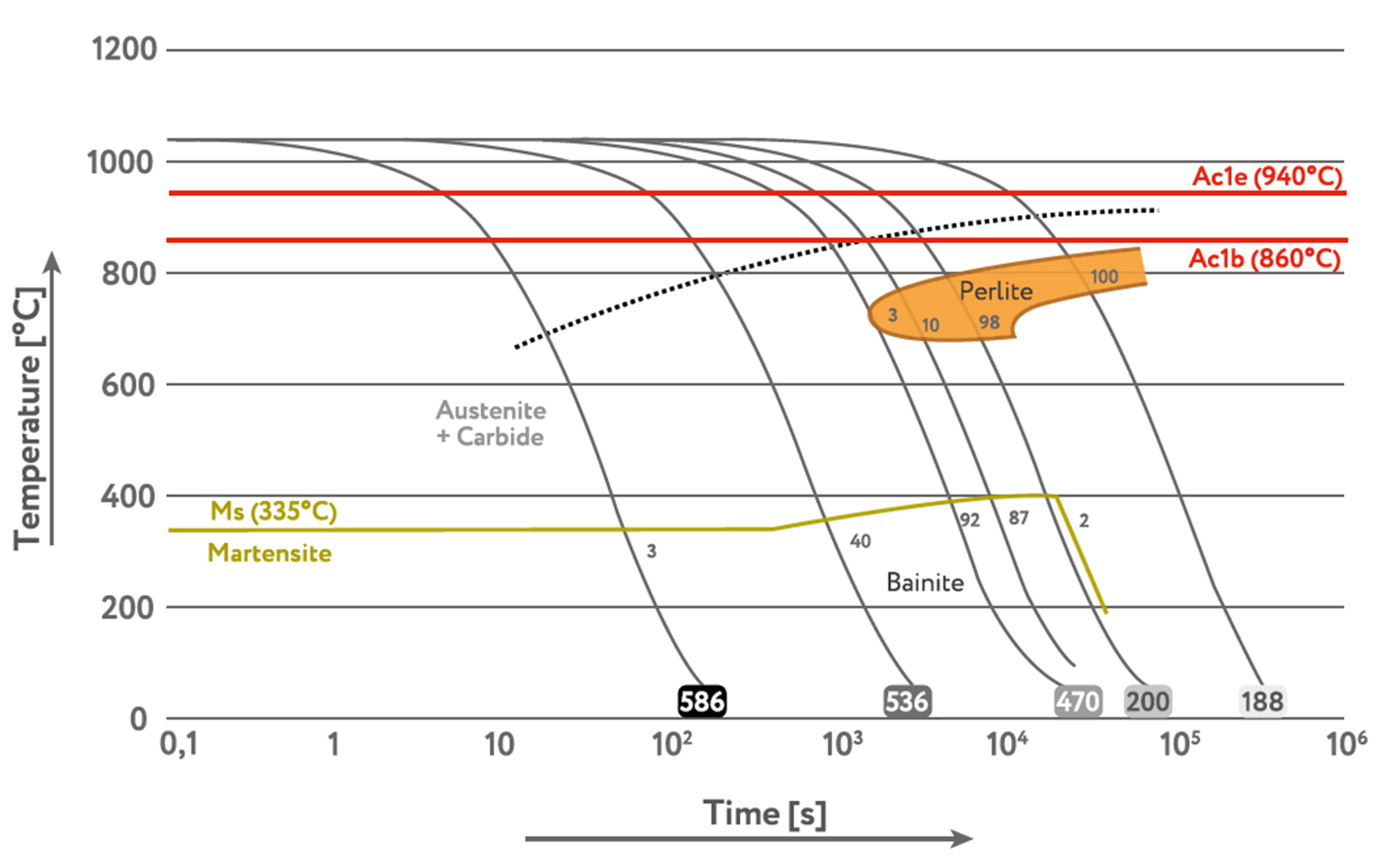
Tempering Curve
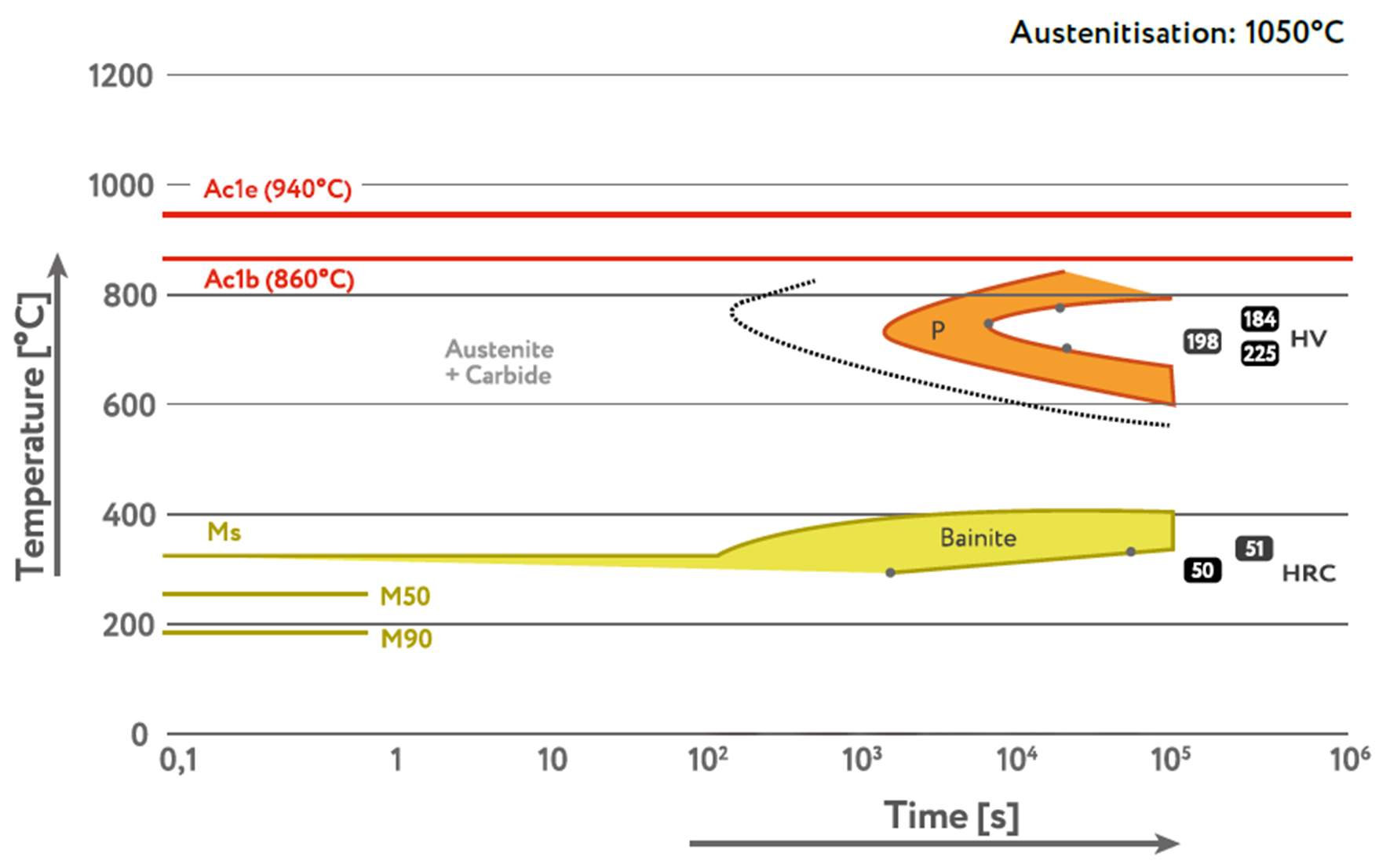